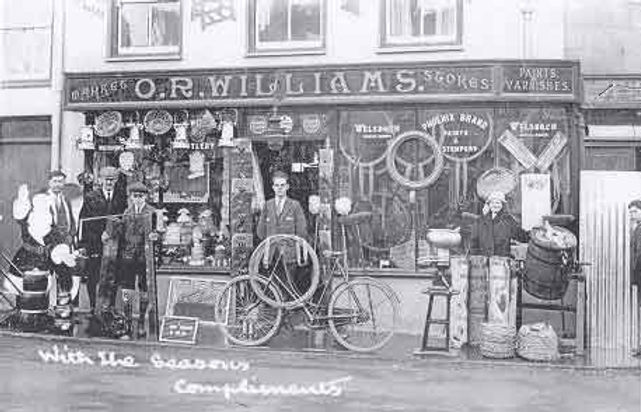
Useful Technical Information
Titanium
The titanium grade we use is Grade 5, also known as Ti6Al4V, Ti-6Al-4V or Ti 6-4, and is the most commonly used grade for automotive and aerospace fastenings.
It has a chemical composition of 6% aluminium, 4% vanadium, 0.25% (maximum) iron, 0.2% (maximum) oxygen, and the remainder titanium. It is significantly stronger than commercially pure titanium while having the same stiffness and thermal properties (excluding thermal conductivity, which is about 60% lower in Grade 5 Ti than in CP Ti). Among its many advantages, it is heat treatable. This grade is an excellent combination of strength, corrosion resistance, weld and fabricability.
This alpha-beta alloy is the workhorse alloy of the titanium industry. The alloy is fully heat treatable in section sizes up to 15mm and is used up to approximately 400°C (750°F). Since it is the most commonly used alloy – over 70% of all alloy grades melted are a sub-grade of Ti6Al4V, its uses span many aerospace airframe and engine component uses and also major non-aerospace applications in the marine, offshore and power generation industries in particular.
Applications: Blades, discs, rings, airframes, fasteners, components, cases, hubs, forgings.
Strengthwise, Grade 5 titanium falls between the metric grades 8.8 and 10.9 (slightly nearer to 10.9). So, even with drilling you still have a bolt at least as strong as the equivalent 8.8 steel version but almost half the weight.

Recommended Torque Specs
for Titanium Fasteners
Use torque values specified by your equipment manufacture, when available. For titanium fasteners the torque values are listed opposite. We recommend anti-seize or moly paste be applied to the threads to reduce the risk of galling.
The importance of correct application cannot be overemphasized. Undertorque can result in unnecessary wear of nuts and bolts as well as the parts they hold together.
When insufficient pressures are applied, uneven loads will be transmitted throughout the assembly which may result in excessive wear or premature failure due to fatigue.
Overtorque can be equally damaging because of failure of the bolt or nut from overstressing the thread areas.